パレート図で対策の優先順位を決める
ここではQCの7つ道具の内の一つパレート図を説明します。これまで職場で発生した施工上の課題や購入品の問題などによる「標準外作業」を、日報や標準作業書に記録してリスト化をする話をしてきました。この表面化した問題をすべて一気に解決したいところですが、限られた時間の中では困難です。また、単発の小さな問題でしたら解決するコストの方が大きくなることもあります。すなわち発生した問題をグループ化して、大きな問題から優先して対処していくことが重要です。そこで役立つのが「パレート図」です。
グループ化のコツは、問題解決手段に着眼する
グループ化は発生した問題を、似た事象毎にまとめます。例えば、「部品納期おくれ」、「部品のひずみ」、「製品のひずみ」などです。ここでコツとしては、何の為にグループ化をしているかを、しっかりと考えることです。できれば一つの解決手段でそのグループの課題を一気に解決したいわけです。逆に言うと、ぱっと見似たような事象でも、解決手段が大きく分かれてしまう場合は、一緒のグループにすべきではありません。例えば、「部品のひずみ」と「製品のひずみ」です。物理的な事象としては同じかもしれませんが、解決手段は大きく異なることが多いです。前者は購入品管理の強化、前者は自社製造方法の改善などになるかと思います。一気に対処することは困難なので、こういう場合は別々に分けます。
安全・品質は忘れない
「パレート図」を作る前に注意すべきことがあります。それは将来に、災害や客先まで波及する品質問題につながりかねない事象が発生していないかと言うことです。現在は大きな問題になっていなくとも、これを放置するわけにはいきません。優先的に対処しましょう。
グラフを作ってみよう
グラフのサンプルを添付します。
まず下段にグループ化した事象を多い順にならべます。なお発生割合が少ないグループはまとめて右側に記載します。左軸はグループ毎の損害時間(手直し時間や、ライン停止時間等)、右軸は累計値です。
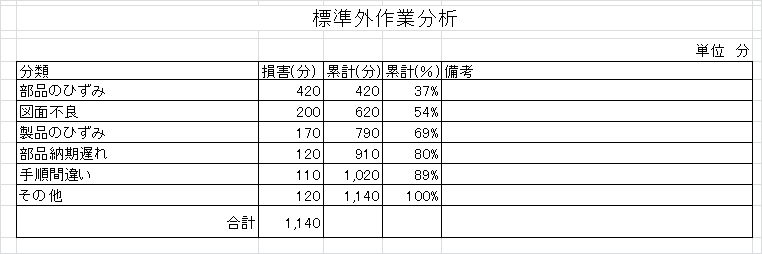
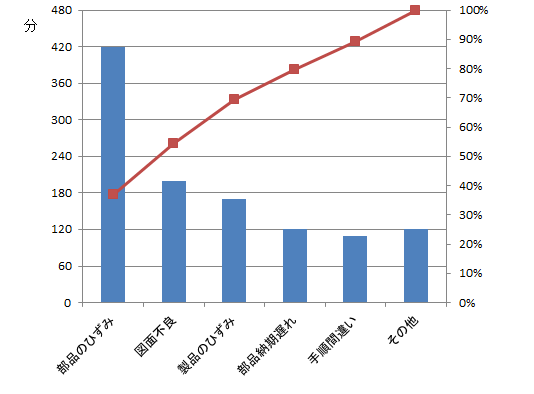
このグラフをもとに左側から優先的に問題をつぶしていきます。そうすることで効率的に改善が行えます。なおここでは、職場での「標準外作業対策」をとりあげましたが、作業改善などにも応用できます。いろいろと活用してみてください。
ディスカッション
コメント一覧
まだ、コメントがありません