動線分析
動線分析は人の動きを、レイアウト図などに図示して可視化したものです。レイアウト改善や工程順序の検討などに役立ちます。添付図を参照ください。
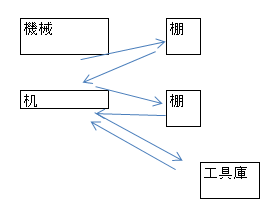
しかし動線分析は、「 ムダな動きが多いね~」の一言で終わってしまうことがよくあります。特に非量産系の職場では、日々役立てています胸を張れるところは少数派かと思います。
悪いレイアウトの現状をみるだけでは意味がない!
特に非量産系では日々生産する製品が変わるので、どうしてもベストだとは言えない設備や棚などの配置の中で作業をせざるを得ないことが多くなります。それを当事者以外が可視化して、「不効率ですね~」と話したらどうなるでしょうか。「わかっている!余計なお世話!!」で、終わってしまうのが普通だと思います。 もちろん当事者自らが可視化した場合は、そんな反応はないでしょう。でも、漠然と見ているだけでは大して結果は変わりません。 現状がボロボロのレイアウトで動線分析をして、悪いことが分かっても仕方がないのです。
まずはレイアウトを改善したい気持ちから
そう、まずは職場を中心としてレイアウトを改善したい気持ちがないと始まりません。そしてレイアウトをどうするかを、真摯に語り合うところがスタートです。そして、実際に作業者をしている人を中心としてベストのレイアウトを真摯に考えるのです。作業者が頻繁に入れ替わる量産ラインでは少し違うかもしれませんが、個別生産や少量生産の職場では、作業者の気持ちやモチベーションが工場全体に影響を与えるほど非常に大きなものがあります。
分析の前に標準化
細やかで精度の高い動線分析をしても、作業のやり方がコロコロと変わっていては分析の意味がなくなります。標準作業を手順書などに記載し運用するしくみが整えるのが先決です。
https://tu-ju.com/category/%e6%a8%99%e6%ba%96%e4%bd%9c%e6%a5%ad/ 標準作業のカテゴリー
置き場所を識別
置き場所にはしっかり識別をすることが大事です。また分析の結果ベストの置き場所がわかったら、その識別場所も変更するようにしましょう。
参考5S(整理整頓…)は職場を効率的状態に戻す活動 https://tu-ju.com/2019/05/03/post-40/
最適解がベストとは限らない
以上がおおまかな動線分析の流れです。動線分析を突き詰めていけば、最適なレイアウトが見えてくるかもしれません。しかし、それ以上に重要なのは職場がレイアウト改善をやろうとする気持ちなのです。動線分析を職場の気持ちを可視化する有力なツールとしてご活用ください。
ディスカッション
コメント一覧
まだ、コメントがありません