効率化をすすめる順序
https://tu-ju.com/2019/05/05/post-99/ ムダと効率の悪さを 意識する
これまで述べた通り、仕事の中の時間の占める割合は、働きが少なくてムダだらけなのが一般的です。量産ラインで仕事をしている方はともかく、非量産系では大きなムダを多少そぎ落とすだけで、ライバルより優位に立てるということがよくあります。では手っ取り早く大きな無駄をなくすにはどうすればいいでしょうか?それには、次のような順番で考えると良いと言われています。
運搬、検査、段取、加工の順に効率化
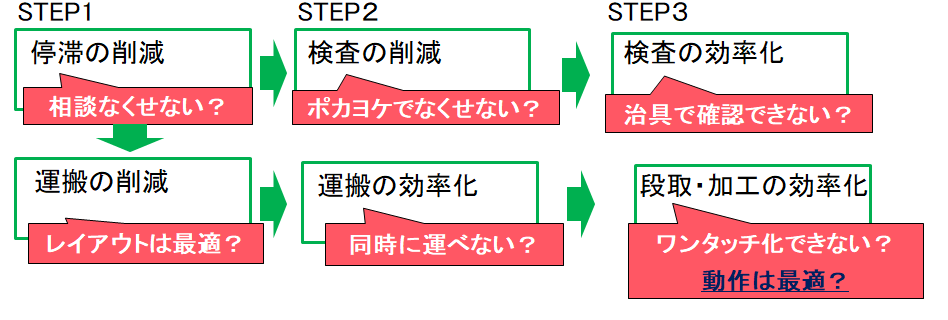
大きなムダをなくすには、 運搬、検査、段取、加工の順にムダをなくして効率化をしていくとやりやすいです。これは左に挙げたものほど大きなムダ潜んでいることが大きいことと、逆転させてやってしまった場合、例えば「加工が効率的になる治具を考えたけど、運搬を減らすためにレイアウト変更したら、新たな場所にはその治具がうまく収まらずに作り直した。」など手戻りが発生しやすいからです。
停滞や運搬・移動を把握する
一般的に一番大きなムダは停滞と運搬や移動だと言えます。理想は止まることなく同じ場所で次々と楽に仕事をこなせる状態にもっていくことです。でも、多くの職場ではしばしば作業が中断したり、部品や工具をとりに動いているのが通常です。まずは、停滞や運搬にどの程度の頻度と時間がかかっているか把握してみましょう。停滞の理由や、作業エリアを離れてとりに行った時間と、何を取りにいったのかをメモしていくのです。
改善を考える順序(ECRSの原則)
次に運搬に時間がかかった割合が大きい順に、
- E:「レイアウト変更等で運搬をなくせいないか」
- C:「一回で運べないか」
- R:「作業順を入れ替える等で効率化できないか」
- S:「治具作成等で運搬を効率化できないか」
と上から順に改善をかんがえてみましょう。
参考:上記の順に改善を考える方法を「ECRSの原則」と呼びます。改善を考える上ではまずはその作業をなくせないかと考え始めることが重要です。なくせる作業のための治具をいきなり作成しても、ムダになっちゃいますよね。
運搬なくしすぎの罠には注意
運搬をなくすことは重要なのですが、運搬をなくすことでそのあとの工程の作業性が低下することがないようには注意してくだい。運搬を減らしたやりにくい状態を我慢して溶接作業をしたために、溶接効率が2~3割低下、品質や安全性も悪くなっていた事例も存在します。
ディスカッション
コメント一覧
まだ、コメントがありません