設備レイアウト改善
工場の設備レイアウトは最初に設置されたままになっていませんか?レイアウトが悪いと、リードタイムが長くなり、移動のムダの発生につながりコストを悪化させてしまいます。それを避けるためには設備レイアウトを最適に保つ必要があります。では、最適な設備レイアウトはどのようなものでしょうか?「自動車工場のようにラインをつくり、ベルトコンベアに乗せられた仕掛品を黙々と組み上げていく形」だと勘違いされていませんか?。その誤解を解いていこうと思います。
そこでまずは工場における主な設備配置形態の長所と短所を述べていきたいと思います。それぞれの製造形態にあった 設備配置を選べば生産効率は向上します。
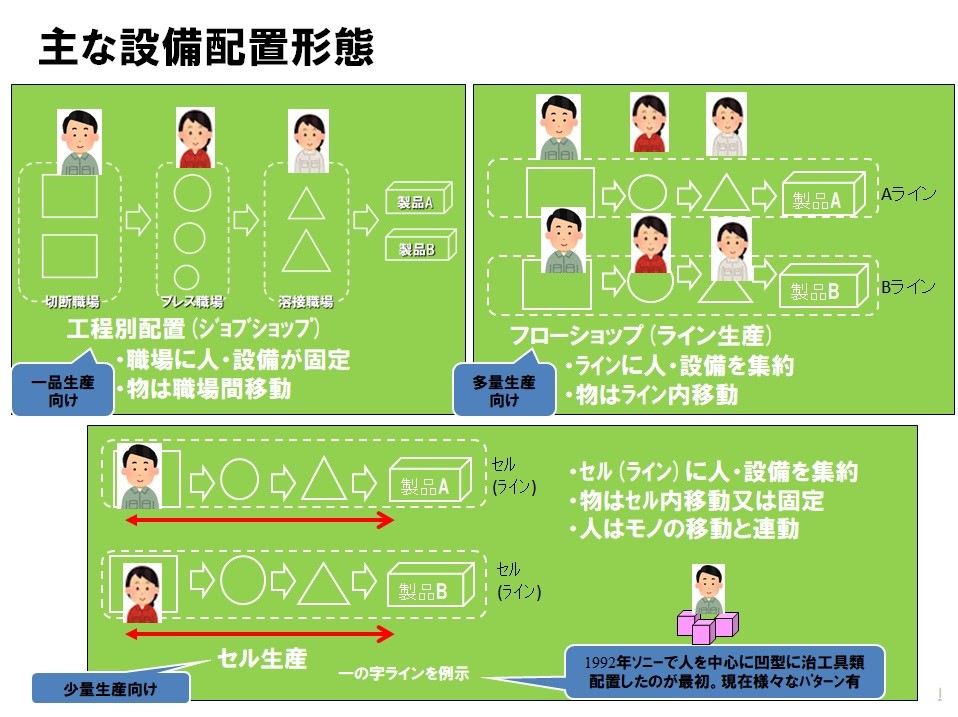
ライン生産(製品別配置)
大手の自動車工場でのベルトコンベアに製品を乗せてくみ上げていく作り方がライン生産です。設備は製品別配置になっています。効率的な生産の代名詞のようになっていますが万能ではありません。およそ次のような特徴があります。
長所
- 仕掛品・部品・治工具類の移動を最小にでき効率的
- 細かく作業担当を分けるので、技能習熟が早い
- みんなでペースを合わせて作るので、ペースの乱れが少なくなり仕掛が少なくなる
- 異常があればラインがとまるので、問題が潜在化しにくい
短所
- ライン状に設備を並べるのに時間とコストがかかる
- 作業を細かくした分だけ多くの作業者が必要
- 少ない作業者ではラインを動かしにくく少量生産が難しい
- 作業が単調になりやすく、作業者のモチベーションがあがりにくい
すなわち、ライン生産は大量生産で最適な生産レイアウトと言えます。
ジョブショップ(工程別配置)
こちらが主に一品生産などに向いたレイアウトです。機械職場、製缶職場、組立職場などを工程別に設備がまとめて配置します。昔ながらの工場のイメージです。多くの町工場はこちらのレイアウトになっていると思います。欠点としては、仕掛製品の工程間移動に時間がかかることなどがあげられます。しかし、一品生産の場合、設備を動かしてラインをつくるよりも仕掛製品を動かした方がよほど効率的です。大量生産が少なくなった日本の多くの工場にマッチするレイアウトとともいえます。
セル生産
1992年ソニーで人を中心に凹型に治工具類配置したのが最初です。本来は一人が製品を最初から最後までくみ上げるやり方でした。限られた単工程を担当する単調なライン生産と違い、多工程を担当するので作業に変化があり単調になりにくい長所があります。少量生産が効率的にできると言われています。しかし、一人ずつに部品や治工具類を配膳しなければならない欠点があります。また優秀な多能工を多く必要になります。ですから現在は本来のセル生産のやり方でなく、少人数で多工程持ちをするI字ラインなど、セル生産の変形バージョンでの生産がよくみられます。
その他設備レイアウト
上記以外には、船舶などで有名なドック方式など様々なバリエーションがあります。ドック方式は大型製品を限られた面積で製造するのに適した手法です。
今回主にとり上げた3つのレイアウトの長所短所を下にまとめます。海外生産等で大量生産が少なくなった日本の多くの工場においては、理想とすべき設備レイアウトはセル生産及び変形バージョンとジョブショップ生産がベースになるかと思います。これらをうまく組み合わせて最適なレイアウトを追求することが重要です。また、様々な製品を多工程にわたって作ることができる多能工技能者の育成が重要となります。
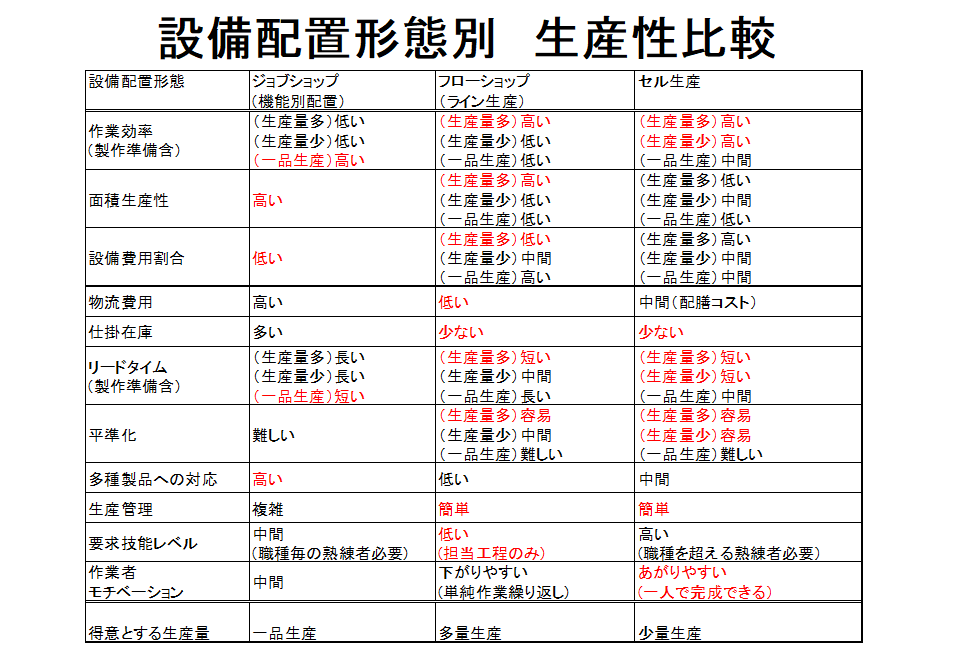
ディスカッション
コメント一覧
まだ、コメントがありません